The aim of the project is to demonstrate the environmentally safe incineration of plastic waste for the production of process heat and co-disposal of animal manure. Innovation: The most important innovative aspects are: a. Incineration of plastic waste in a fluidized bed b. Incineration of animal manure in a fluidized bed c. Co-disposal of plastic waste and animal manure. The energy production can be seen as follows : Plastic waste + animal manure combustion results to a net energy production of 123,040 GJ/y. This energy is used for various drying processes during recycling of plastic waste and drying of animal manure with total requirement of 109.522 GJ/y. The rest will be used for stable heating. This corresponds to a cost of 8.34 MBEF/year. Other cost savings are dumping costs and transportation costs of the plastic waste and the animal manure corresponding to 24.20 MBEF/year Custom made small fluidized bed incinerators for plastic waste are not known to exist at present. As far as the proposers are concerned, it is the first time that a fluidized bed incinerator will be used for the incineration of pig manure. Furthermore there is no known process where plastic waste and animal manure (or any other effluent stream) are codisposed, in situ. Ravago Plastics NV is active in the recycling of specific industrial plastic wastes. The Arendonk plant has a very efficient recycling facility but currently some 15 ton/day of residual non-recycle waste is dumped. The incineration of the waste for energy recuperation is the subject of this project. At current dumping costs, Ravago Plastics spends 8.16 MBEF/y for waste disposal. In view of rising dumping charges, future costs will exceed 18.000.000 BF/y. Since Ravago Plastics has specific energy requirements for its plant operations i.e. dryer fuel, a combined waste combustor/boiler and associated steam distributionsystem will be installed. MOONS (which is active in intensive plg raising industry with an annual production of 15000 animals/year) could co-treat its manure within the RP unit (where excess heat is available), resulting to extensive savings given below: - 325,470 l of gasoil/year for transport, spreading of the manure, as well as for the stable heating. - 4 man-year of associated labour - 3.00 MBEF/year for manure disposal charges (as per Decree and current taxation-rates). In an effort to reduce the manure to be discharged, and in view of the excess energy produced in the RP combustor-boiler plant, a thermal linking of RP and MO appears to offer a potential for solving the waste disposal problem for both companies.
Want to analyze based on this project via our analysis tool? Analyze this project
Knowledge Gaps
Environmental fate and behavior of plastic
Commercial-related uncertainties
Environmental risk assessment (ERA)
Environmental exposure
Environmental effects and ecotoxicity
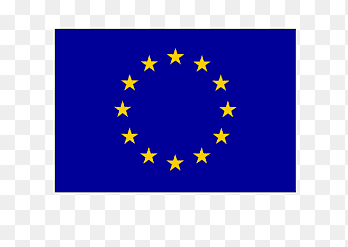